Objetivo :
Apresentar as técnicas e fundamentos básicos que orientam a bom desenvolvimento do Projeto
de Molde Plástico, nas etapas de concepção do projeto, escolha de matéria-prima., tipos de moldes,
contração, escolha de cavidades, Sistema de Alimentação, Sistema de Refrigeração, Sistema de
Extração, Saída de Gases, escolha de Aços para Moldes e Design de peças e tryout das mesmas.
Destina-se :
A técnicos que trabalham na operação de produção, preparadores DE MÁQUINAS,
engenheiros e administradores ligados a área de processo de fabricação e desenvolvimento
e qualificação de fornecedores
Metodologia :
O curso será apresentado com base em teoria, discussões de casos, e apresentação
de solução de problemas, exemplos práticos do instrutor,
Programa :
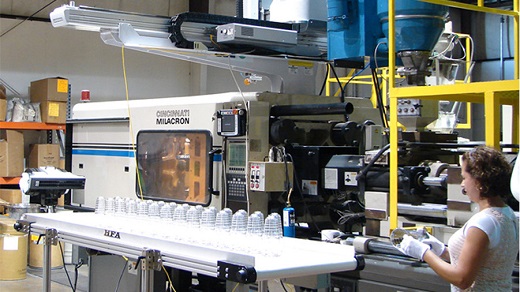
I – Matéria-Prima.
História do desenvolvimento dos Plásticos, Fontes de Matérias Primas: fontes naturais
e Petróleo, Classificação dos Polímeros: termoplásticos, termofixos e elastômeros,
Propriedades dos Polímeros, Plásticos Convencionais/commodities, Plásticos de Engenharia,
Secagem de matéria-prima:
II – Moldes :
1 - Introdução.
2 - Definição do número de cavidades.
3 - Máquina Injetora:
Noções sobre processo de Injeção, Força de fechamento, Distância entre colunas, Volume ou
capacidade de Injeção, Tempo de residência no canhão.
4 - Contração.
5 - Tipos de molde.
Molde de Injeção de duas Placas, Molde de Injeção de três Placas, Moldes de Injeção com
Placas Móveis (Gavetas), Molde com Núcleo Rotativo, Sobre-injeção.
6 - Disposição das cavidades.
7 - Sistema de alimentação.
Sistema de alimentação direta, Entrada Direta com Bico ou Câmara Quente.
8 - Sistema de alimentação.
Entrada restrita circular ou retangular, Entrada em leque, Entrada tipo Flash, Entrada Capilar,
Entrada em Aba, Entrada Submarina, Entrada em anel ( Diafragma), Entrada Direta,
Entrada por bico Quente, Entrada por Câmara Quente.
09 – Sistemas de refrigeração.
Noções sobre troca térmica.
10 – Sistemas de extração.
Extração por ar comprimido, Sistema de extração por placa extratora, Sistema de Extração por Pinos,
Sistema de Extração por Placa, Sistema de Extração por Laminas, Sistema de Extração por Tirantes
e por Correntes, Sistema de extração por núcleo rotativo.
11 – Saída de Gases.
Efeito diesel.
12 – Aços para Moldes.
Aços, Diferentes Partes do Molde, Molde com Gavetas, Pinos e Pinças, Fator Econômico,
Abrasividade, Oxidação, Tratamento Térmico, Envelhecimento, Têmpera, Tratamento de Superfície,
Nitretação.
13 – Design de peças
Ângulos de Saída e Conicidade, Espessura de parede, Nervuras, Ângulos Vivos ou Cantos Vivos,
14 – Tryout de Peças
Check List para liberação do ferramental, Check List para liberação para Try Out, Preparativos
para o Try Out, Secagem do material, Definição do sistema de refrigeração, Data Sheet da Matéria
Prima, A escolha da Máquina Ideal, Dimensionamento do diâmetro do bico injetor.
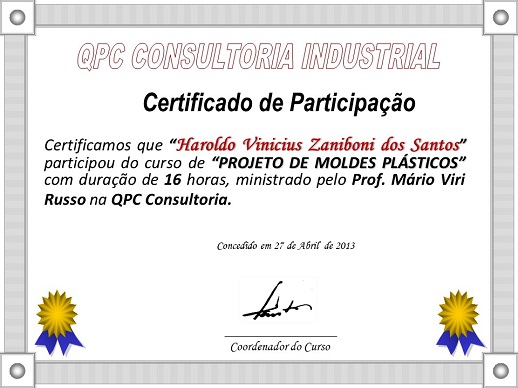
Apresentador(es) :
MÁRIO VIRI RUSSO
Graduado em Tecnologia em Polímeros pela Faculdade Oswald Cruz., Pós Graduado em Gestão de Produção pelo IMES, Graduação em Bacharel em Desenho Industrial pela Universidade São Judas Tadeu, com habilitação em desenvolvimento de projeto de produto, Técnico em Plásticos pela Escola Senai Mário Amato.
EXPERIÊNCIA PROFISSIONAL – Desenvolve atividades nas áreas de Engenharia, Processo e Projetos de Injeção e Montagem de peças Plásticas em empresas como SIEMENS VDO AUTOMOTIVE LTDA, CIBIÊ DO BRASIL LTDA (VALEO), REVLON BOZZANO LTDA. PROJETOS ESPECIAIS :
1 - Coordenador e consultor técnico no desenvolvimento e construção da planta de injeção no complexo industrial GM em Gravataí- RS, destinada ao projeto Celta II, dando suporte pela Siemens VDO Automotive à empresa IPA, na escolha e aquisição dos maquinários de injeção de peças plásticas (2200 – 300 ton), seus periféricos como desumidificadores, trocadores de calor e aquecedores, juntamente com toda a análise de projeto de ferramental de injeção, desde o estudo de FMEA de projeto, execução, Try Out e aprovação do produto final junto ao cliente GMB.
2 - Coordenação de Novos Projetos na Siemens VDO, na implantação da linha de montagem dos seguintes produtos: Coletor de ar Honda Fit (Intake Manifold), Tampa comando de Válvulas GMB (Vectra, Corsa e Brava), que englobaram desde o desenvolvimento dos ferramentais de injeção, dispositivos de solda vibracional, inserção a quente de insertos metálicos e dispositivos de controle final de